Difference between revisions of "Fish guidance structures with narrow bar spacing"
Bendikhansen (talk | contribs) |
Bendikhansen (talk | contribs) |
||
Line 59: | Line 59: | ||
This article describes several different types of fish guidance structures with narrow bar spacing. The classification table does not represent all of them for every topic. Therefore, an additional table is added to highlight where and how the types differ. | This article describes several different types of fish guidance structures with narrow bar spacing. The classification table does not represent all of them for every topic. Therefore, an additional table is added to highlight where and how the types differ. | ||
− | + | {| class="wikitable" style="vertical-align:bottom;" | |
+ | |- | ||
+ | ! | ||
+ | ! style="background-color:#efefef;" | Vertically inclined bar rack (VIBR/VIPP) | ||
+ | ! style="background-color:#efefef;" | Angled vertical bar rack (AVBR) | ||
+ | ! style="background-color:#efefef;" | Angled vertical streamwise bar rack (AVSBR) | ||
+ | ! style="background-color:#efefef;" | Angled horizontal bar rack (HBR) | ||
+ | |- | ||
+ | | style="background-color:#efefef;" | Fish species | ||
+ | | Tested on: smolt, European eel | ||
+ | | Tested on: smolt, European eel | ||
+ | | N/A | ||
+ | | All | ||
+ | |- | ||
+ | | style="background-color:#efefef;" | Power losses | ||
+ | | Low head loss and symmetrical turbine admission flow | ||
+ | | High head loss and mild assymetric turbine admission flow | ||
+ | | Low head loss and symmetrical turbine admission flow | ||
+ | | Low head loss and quasi-symmetrical turbine admission flow | ||
+ | |- | ||
+ | | style="background-color:#efefef;" | Certainty of effect | ||
+ | | Very certain | ||
+ | | Very certain | ||
+ | | Moderately certain | ||
+ | | Very certain | ||
+ | |- | ||
+ | | style="background-color:#efefef;" | TRL | ||
+ | | 9 | ||
+ | | 9 | ||
+ | | 4 | ||
+ | | 9 | ||
+ | |} | ||
{{Fish guidance structures with narrow bar spacing}} | {{Fish guidance structures with narrow bar spacing}} |
Revision as of 15:41, 26 January 2021
Contents
Introduction
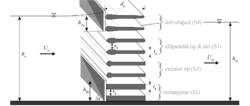
Different measures are used to protect downstream moving fish (details in FIThydro deliverable 2.1) at hydropower plants and water intakes, of which two different fish guidance structures (FGSs) with narrow bar spacing were investigated within the FIThydro project: (I) inclined bar racks and (II) horizontal bar racks.
Inclined bar racks
Vertically Inclined Bar Racks (VIBR) consist of plane screens composed of elongated flat bars positioned in vertical planes aligned with the flow (Figure 1). The plane screen is inclined with an angle β with respect to the river bed in order to guide fish towards one or several surface bypasses located at the top of the rack (Raynal et al., 2013a). Another configuration consists of a perforated plate, which is called Vertically Inclined Perforated Plate (VIPP). Detailed information on the design and efficiency of both VIBR and VIPP is given in the FIThydro Deliverable 3.4 and Lemkecher (2020).
Angled bar racks
Angled bar racks are installed at an angle α to the flow direction in plan view to guide fish towards a bypass located at the downstream end of the rack. Three types of angled racks with narrow bar spacing can be distinguished (Figures 2, 3 and 4):
- Classical” angled bar rack, with vertical bars angled with γ = 90°- α (cf Figure 2, (Raynal et al, 2013b)
- Angled bar rack with vertical bars oriented in the streamwise direction (γ = 0°) (cf. Figure 2) (Raynal et al., 2014).
- Horizontal Bar Rack - Bypass System (HBR)’ (Figures 2, 3 & 4) (FIThydro deliverable 3.4, 2020; Albayrak et al., 2019; Lemkecher et al., 2020b; Meister, 2020; Meister et al., 2020a, b).
These rack structures are designed as physical fish exclusion and guidance barriers and may act as behavioral barriers depending on the bar spacing and fish size. The lower the bar spacing, the higher the fish will be reluctant to go through the rack. As a rule of thumb, the rack constitutes a physical barrier when the bar spacing is lower than 1/10 of the total length for most species including salmonids, but except for eels, which require bar spacing lower than 3% of their length (Ebel, 2016).
Figure 3 shows the horizontal bar rack – bypass system (HBR-BS) of the FIThydro case study residual HPP Schiffmühle at Limmat River, Switzerland, during revision work in 2018. The design discharge of the HPP is Qd = 14 m3/s and the HBR-BS was built in 2013 with foil-shaped bars, a clear bar spacing of sb = 20 mm, and a pipe bypass.
Description of VIBRs and HBRs
Vertically inclined bar racks (VIBR) and horizontal bar racks (HBRs) are physical barriers which prevent fish from entering the turbines at run-of-river HPPs. VIBRs and HBRs are characterized by narrow bar spacings ranging between 10 and 30 mm, such that they are physically impermeable for majority large share of the fish population (Figures 2 and 3; Meister et al., 2020). Bottom and top overlays can be used to enhance the guidance efficiency of sediments, floating debris, and bottom and surface oriented fish (Figure 4). An automated rack cleaning machine is needed to prevent the rack from clogging. Figure 4 illustrates that the bypass discharge is usually controlled with a restrictor and a ramp.
The bars of VIBRs and HBRs can be built with different bar shapes, such as rectangular, rectangular with a circular tip, rectangular with an ellipsoidal tip & tail, and foil-shaped (Figure 5). Most modern HBRs are equipped with foil-shaped bars or rectangular bars with an ellipsoidal tip & tail because of the reduced head losses (Meister et al., 2020a, Lemkecher et al. 2020a). Additionally, these bars can be cleaned easier than rectangular bars due to the thickness reduction from tip to tail (Meister et al., 2018). Figure 5 shows the different rack parameters of an HBR, including the clear bar spacing sb, the bar thickness tb, and the bar depth db (see FIThydro deliverable 3.4 for more information on HBR-BS)
Methods, tools, and devices
During planning
To prevent fish from passing through the FGS with narrow bar spacing, there are three design criteria: the bar spacing, the normal velocity (Vn; velocity component normal to the rack axis), which is directly linked to the rack surface, and the ratio of the rack parallel velocity (Vp) to the rack normal velocity, which should be higher than 1, i.e. Vp/Vn >1. The maximum values of the first two parameters depend on the species taken into account. The recommended bar spacing and normal velocity (Vn ) are the same for inclined racks (VIBR), angled racks with horizontal bars (HBR) and with vertical streamwise bars, as the “louver effect” is not considered strong enough in such configuration. For salmonid smolts, the bar spacing (for inclined and angled bar racks) has to be smaller than 10-15 mm to constitute a physical barrier (1/10 of body width). As eels do not show strong behavioural repulsion and are therefore likely to pass through the racks, it appeared necessary to implement physical barriers. In France, the recommended bar spacing (for inclined and angled bar racks) is generally 20 mm to stop female eels longer than 50-60 cm. The bar spacing can be reduced to 15 mm in case of a significant presence of males upstream of the HPP (Courret, et al., 2008).
For HBRs, the horizontal approach flow angle α, is selected such that the velocity component normal to the rack Vn does not exceed the sustained swimming speed of the target fish species. Approach flow velocities, typically varying between Uo = 0.40 and 0.80 m/s, lead to α = 20÷40°. The rack angle is therefore a compromise between limiting Vn on the one hand and the rack length on the other hand. For Vertically Inclined Bar Racks (VIBRs), rack inclinations of the order of 25° are favourable to fish guidance – thus confirming existing recommendations - and helping to limit the head losses (Courret and Larinier, 2008; Courret et al., 2015). The head losses induced by HBRs can be predicted with the equations published in Meister et al. (2020a). These equations do not only take rack parameters, as defined in Figure 5, into account, but also different approach flow configurations as determined by the HPP layout such as diversion HPP or block-type HPP. If an HBR is installed in the headrace channel of a diversion HPP, the velocities are typically nearly equally distributed, which means that the criterion of Vp/Vn > 1 is fulfilled for HBRs with α < 45° (Meister et al., 2020b). If an HBR is installed at a block-type HPP, the streamline pattern is usually complex and Vp/Vn along the rack decreases towards the downstream rack end (Meister et al., 2020b). Likewise, Vn will be underestimated at the downstream rack end if the velocity components are calculated from continuity, which could lead to fish impingements. It is therefore recommended to determine the optimal HBR position with a numerical simulation such as described in Feigenwinter et al. (2019).
The head losses of VIBRs and VIPP can be predicted using the equations developed by Lemkecher (2020). In addition to the design of a FGS with narrow bar spacing, the bypass design is important to safely collect and transport the fish and to return them unharmed to the river downstream of an HPP. Different bypass designs are described in literature such as the full depth open channel bypass, a bypass with a bottom and top opening, and a pipe bypass. The latter is not recommended because it can clog easily and fish avoid large velocity gradients at the inlet of the pipe bypass (Beck et al., 2020). Design of the bypass for VIBR and VIPP is described in the FIThydro Deliverables 2.2 and 3.4.
The height and the width of the turbine intake influences the choice of the solution (inclined or angled). In addition, the possible location of the bypasses could modify the final solution. To reduce head losses, a particular attention has to be paid on the bar shape, the spacers and the support of the bar rack. For more details, please see the FIThydro Deliverables 2.2 and 3.4; and Fish guidance structures with wide bar spacing.
During implementation
The installation of fish guidance racks requires heavy lifting equipment and both the fixing and the placing of the structure requires a shut-down of the hydropower plant and the dewatering of the headrace channel or water intake (Figure 6). Installation of racks and a bypass system requires a suite of skilled labor on civil works.
During operation
After the installation of a FGS with narrow or wide bar spacing, the velocity field should be measured (e.g. with an Acoustic Doppler current profiler (ADCP)) in front of the FGS, at the bypass inlet, and in the bypass for different load cases. In parallel, a fish monitoring campaign, using radio/acoustic telemetry or PIT-tagging is recommended to assess the fish protection and guidance efficiency of the FGS (FIThydro Deliverable 2.2). Efficiencies between 80% and 100% for eels and smolts are considered satisfactory. This can reduce the global mortality at a HPP to values of about 1-2% or even less, taking into account the movements via the spillway and survival rates when passing through the turbines (Tomanova, et al., 2018). The results of the monitoring campaign can be used to optimize the operation of the FGS, especially the operation of the bypass.
Reducing the bar spacing of the rack increases its blockage ratio and thus head losses. In addition, the rack is more quickly clogged by trash and organic fine material and hence cleaning during seasons of high floating debris transport poses a challenge. It is particularly crucial to avoid a permanent clogging by debris, which cannot be removed by the cleaning machine. Therefore, the hydraulic head losses of a FGS should be continuously measured and compared to the predictions calculated prior to construction. The head loss measurements should be also used to determine the flushing intervals of the bypass. That is, if a certain threshold value of the head losses is exceeded, the rack cleaning machine should start its operation automatically, and the bypass is opened to flush sediments and floating debris.
Relevant MTDs and test cases
Classification table
This article describes several different types of fish guidance structures with narrow bar spacing. The classification table does not represent all of them for every topic. Therefore, an additional table is added to highlight where and how the types differ.
Vertically inclined bar rack (VIBR/VIPP) | Angled vertical bar rack (AVBR) | Angled vertical streamwise bar rack (AVSBR) | Angled horizontal bar rack (HBR) | |
---|---|---|---|---|
Fish species | Tested on: smolt, European eel | Tested on: smolt, European eel | N/A | All |
Power losses | Low head loss and symmetrical turbine admission flow | High head loss and mild assymetric turbine admission flow | Low head loss and symmetrical turbine admission flow | Low head loss and quasi-symmetrical turbine admission flow |
Certainty of effect | Very certain | Very certain | Moderately certain | Very certain |
TRL | 9 | 9 | 4 | 9 |
Classification | Selection |
---|---|
Fish species for the measure | All |
Does the measure require loss of power production | Operational (requires flow release outside turbine) |
- | |
- | |
Recurrence of maintenance | Yearly |
Which life-stage of fish is measure aimed at | - |
- | |
- | |
Movements of migration of fish | |
Which physical parameter is addressed | N/A |
- | |
- | |
- | |
- | |
- | |
- | |
- | |
Hydropower type the measure is suitable for | Plant in dam |
Plant with bypass section | |
Dam height (m) the measure is suitable for | Up to 10 |
Section in the regulated system measure is designed for | In dam/power plant |
- | |
- | |
- | |
River type implemented | Steep gradient (up to 0.4 %) |
Fairly steep with rocks, boulders (from 0.4 to 0.05 %) | |
Slow flowing, lowland, sandy (less than 0.05 %) | |
Level of certainty in effect | Very certain |
Technology readiness level | TRL 9: actual system proven in operational environment |
Cost of solution | See cost table |
Relevant literature
- Albayrak, I., Kriewitz, C.R., Hager, W.H., Boes, R.M. (2018). An experimental investigation on louvres and angled bar racks. Journal of Hydraulic Research, 56(1): 59-75, https://doi.org/10.1080/00221686.2017.1289265.
- Albayrak, I.; Maager, F.; Boes, R.M. (2019). An experimental investigation on fish guidance structures with horizontal bars. Journal of Hydraulic Research, 58(3): 516-530.
- Albayrak, I., Boes, R.M., Kriewitz-Byun, C.R., Peter, A., Tullis, B.P. (2020). Fish guidance structures: new head loss formula, hydraulics and fish guidance efficiencies. Journal of Ecohydraulics, https://doi.org/10.1080/24705357.2019.1677181.
- Beck, C. (2020). Fish protection and fish guidance at water intakes using innovative curved-bar rack bypass systems. VAW-Mitteilung 257 (R.M. Boes, ed). VAW, ETH Zurich, Switzerland. https://vaw.ethz.ch/en/the-institute/publications/vaw-communications/2010-2019.html
- Beck, C., Albayrak, I., Meister, J., Boes R.M. (2020a). Hydraulic performance of fish guidance structures with curved bars: Part 1: Head loss assessment. Journal of Hydraulic Research,58(5): 807-818, https://doi.org/10.1080/00221686.2019.1671515.
- Beck, C., Albayrak, I., Meister, J., Boes R.M. (2020b). Hydraulic performance of fish guidance structures with curved bars: Part 2: Flow fields. Journal of Hydraulic Research, 58(5): 819-830, https://doi.org/10.1080/00221686.2019.1671516.
- Courret, D., Larinier M. (2008). Guide pour la conception de prises d’eau “ichtyo-compatibles” pour les petites centrales hydroélectriques [Guide for the design of fish-friendly intakes for small hydropower plants]. France: Agence de l’Environnement et de la Maîtrise de l’Energie (ADEME). Report No: RAPPORT GHAAPPE RA.08.04. http://www.onema.fr/IMG/pdf/2008_027.pdf (in French).
- Courret, D., Larinier, M., David, L., Chatellier, L. (2015). Development of criteria for the design and dimensioning of fish-friendly intakes for small hydropower plant. Fish Passage 2015, Groningen, June 22-24.
- Ebel, G. (2016). Fish Protection and Downstream Passage at Hydro Power Stations — Handbook of Bar Rack and Bypass Systems. Bioengineering Principles, Modelling and Prediction, Dimensioning and Design. ISBN 9783000396861. 2nd edn. Büro für Gewässerökologie und Fischereibiologie Dr. Ebel, Halle (Saale), Germany [in German].
- Feigenwinter, L.; Vetsch, D.F.; Kammerer, S.; Kriewitz, C.R.; Boes, R.M. (2019). Conceptual Approach for Positioning of Fish Guidance Structures Using CFD and expert knowledge. Sustainability, 11(6), 1646. https://www.doi.org/10.3390/su11061646
- FIThydro Deliverable 2.2 (2019). Working basis of solutions, models, tools and devices and identification of their application range on a regional and overall level to attain self-sustained fish populations. https://www.fithydro.eu/deliverables-tech/.
- FIThydro Deliverable 3.4 (2020). Enhancing and customizing technical solutions for fish migration. https://www.fithydro.eu/deliverables-tech/.
- Lemkecher, F., Chatellier, L., Courret, D., David, L., (2020a). Experimental study of fish-friendly angled trash racks with horizontal bars. Journal of Hydraulic Research (in revision)
- Lemkecher F. ; Chatellier L. ; Courret D. ; David L., (2020b). Contribution of different elements of inclined trash racks to head losses modelling. Water, 12(966). https://doi.org/10.3390/w12040966
- Lemkecher F. (2020). Étude des grilles des prises d’eau ichtyocompatibles. Thesis of University of Poitiers, France.
- Meister, J.; Fuchs, H.; Boes, R.M. (2018). Hydraulische Laboruntersuchungen horizontaler Fischleitrechen (‘Hydraulic laboratory investigations of horizontal fish guidance racks’). zekHydro, 15(2): 54–56. http://dx.doi.org/10.3929/ethz-b-000295001[in German].
- Meister, J. (2020). Fish protection and guidance at water intakes with horizontal bar rack bypass systems. VAW-Mitteilung 258 (R.M. Boes, ed.). Laboratory of Hydraulics, Hydrology and Glaciology, ETH Zurich, Switzerland.
- Meister, J.; Fuchs, H.; Beck, C.; Albayrak, I.; Boes, R.M. (2020a). Head Losses of Horizontal Bar Racks as Fish Guidance Structures. Water, 12(2): 475. http://dx.doi.org/10.3390/w12020475.
- Meister, J.; Fuchs, H.; Beck, C.; Albayrak, I.; Boes, R.M. (2020b). Velocity Fields at Horizontal Bar Racks as Fish Guidance Structures. Water, 12(1): 280. http://dx.doi.org/10.3390/w12010280.
- Raynal, S., Chatellier, L., Courret, D., Larinier, M., & Laurent, D. (2013a). An experimental study on fish-friendly trashracks - Part 2. Angled trashracks. Journal of Hydraulic Research, 51(1): 67-75.
- Raynal, S., Chatellier, L., Courret, D., Larinier, M., & Laurent, D. (2013b). An experimental study on fish-friendly trashracks - Part 1. Inclined trashracks. Journal of Hydraulic Research, 51(1), 56-66.
- Raynal, S., Châtellier, L., Courret, D., Larinier, M., David, L. (2014): Streamwise bars in angled trashracks for fish protection at water intakes. Journal of Hydraulic Research, 52 (3), 426-431.
- Tomanova, S. et al. (2018). Protecting Efficiently Sea-migrating Salmon Smolts from Entering Hydropower Plant Turbines with Inclined or Oriented Low Bar Spacing Racks . Ecological Engineering 122, p. 143-152. DOI : 10.1016/j.ecoleng.2018.07.034.
- Turnpenny, A.W.H.; O’Keeffe, N (2005). Screening for Intake and Outfalls: a best practice guide. Technical Report SC030231, Environment Agency, Bristol, United Kingdom.